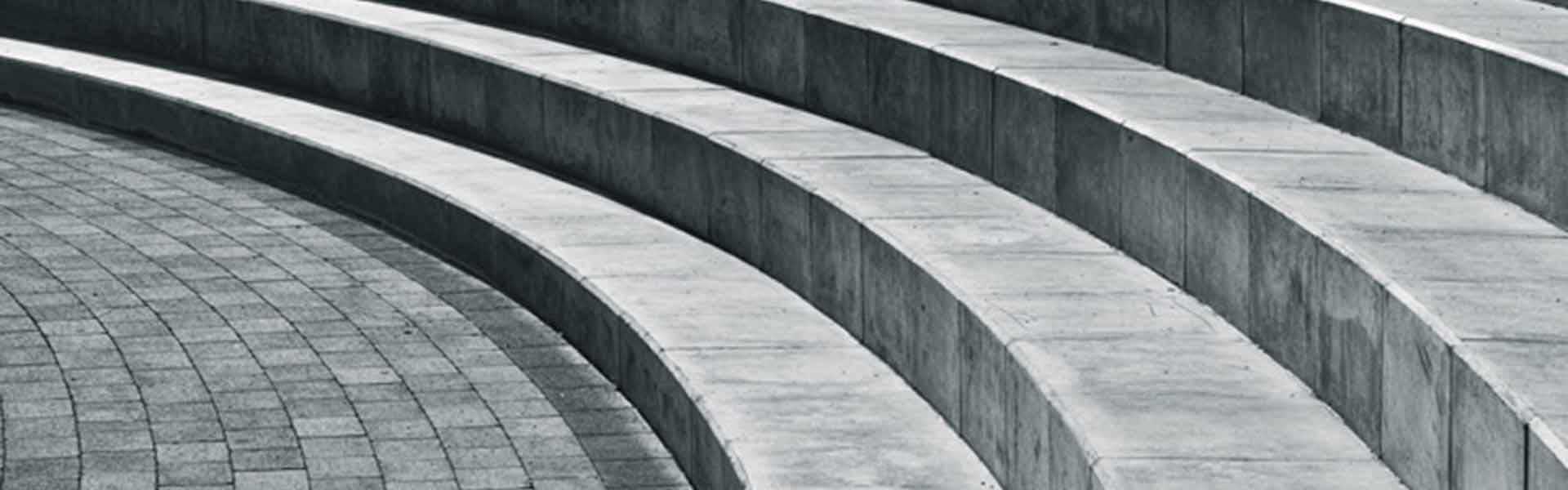
Carbocolor® carbon black offers the concrete construction industry superior depth of color and color retention. Its large particle size and chemical inertness provide significant resistance to long-term weathering and aging, acids, alkalis and heat. Typical applications include paving stones (pavers) and roof tiles, as well as various cements and mortars.
CARBOCOLOR
Thermax®
Click for details
Thermax® CARBOCOLOR is a concrete colorant used to give a dark grey color with blue undertone
Thermax® Carbocolor®
Concrete Colorant
Thermax® Carbocolor® is a concrete colorant used to give a dark grey color with blue undertone.
In lab testing, Carbocolor® has shown to provide superior UV light resistance to concrete versus iron oxide.
Carbocolor® represents a promising alternative to iron oxides and other carbon blacks. Its large particle size makes it a much more suitable concrete pigment than any other carbon black. Its inert nature gives it colour stability not found in iron oxides.
The Thermax® Advantage
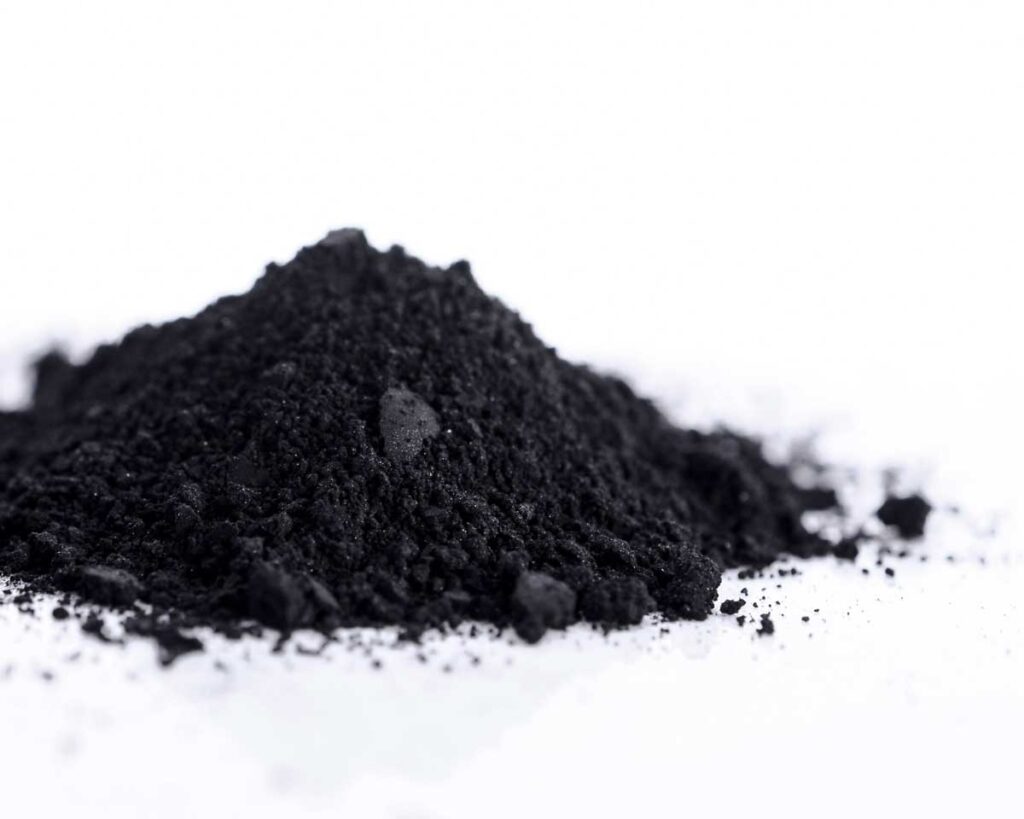
Thermal carbon black is manufactured by the thermal decomposition of natural gas. The thermal process provides a unique carbon black characterized by a large particle size and low particle aggregation which differs from the carbon black grades produced by the furnace black or lamp black processes. Cancarb thermal black is currently used in a wide variety of applications, from rubber and plastic products to metallurgical carbides and other advanced materials, due to its high purity.
The benefits of Thermax® N990 and Carbocolor in concrete include:
- Improved weathering resistance
- No visible signs of pigment migration
- No oxidation or reduction of pigment
- Excellent grey to black coloring with blue undertone
Applications for Carbocolor® include:
- Driveways, sidewalks, and retaining walls
- Coloured masonry products such as paving stones, block, and bricks
- Concrete roofing tile
- Precast products such as bird baths and fountains
- Curbstones

CARBOCOLOR® Lab Results
UV Light Testing
The services of a Canadian Standards Association approved laboratory, Powertech of Vancouver, Canada, were retained to perform comparative UV light resistance testing of Carbocolor® and iron oxide over 500 hours. The following ASTM test methods were performed:
- ASTM G53 – Practice for Operating Light Exposure Apparatus (Carbon-Arc Type) With and Without Water for Exposure of Nonmetallic Materials
- ASTM D2244 – Spectrophotometric Method of Measuring Color Differences in Exposed and Unexposed Specimens. Uses Illuminant D, Hunter Lab scale with specular component.
In the Hunter Lab color space, L represents the dark-light component, a represents the green-red component, and b represents the blue-yellow component. It was found that differences in a and b were insignificant; thus the changes in L explained nearly all of the total colour differences (delta E) of the samples. In the tests performed by Powertech, the samples were not subjected to any weathering other than UV radiation.
Figure 1 shows a plot of delta E with respect to the pigment weight percentage. The tests demonstrate that Carbocolor® has superior UV light resistance characteristics in concrete, especially at higher loadings. Note the high degree of fading found in the uncoloured control sample; the fading of concrete alone could play a significant role in the fade resistance of the coloured samples.
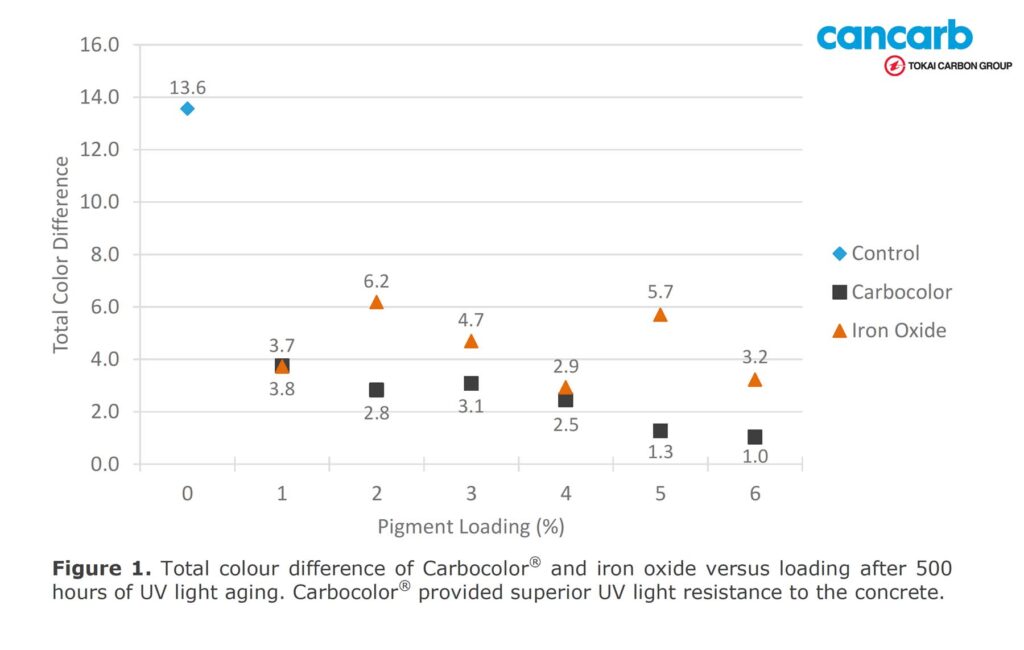
Concrete Water Immersion and Accelerated Weathering Testing
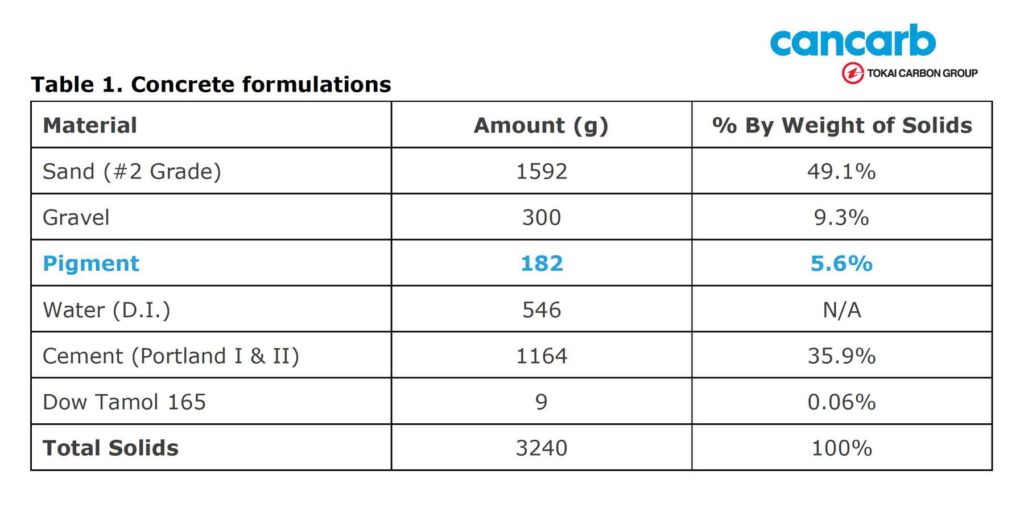
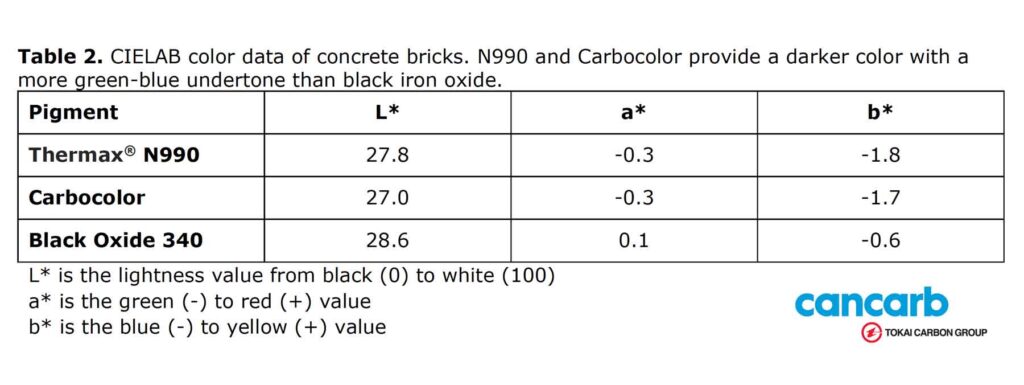
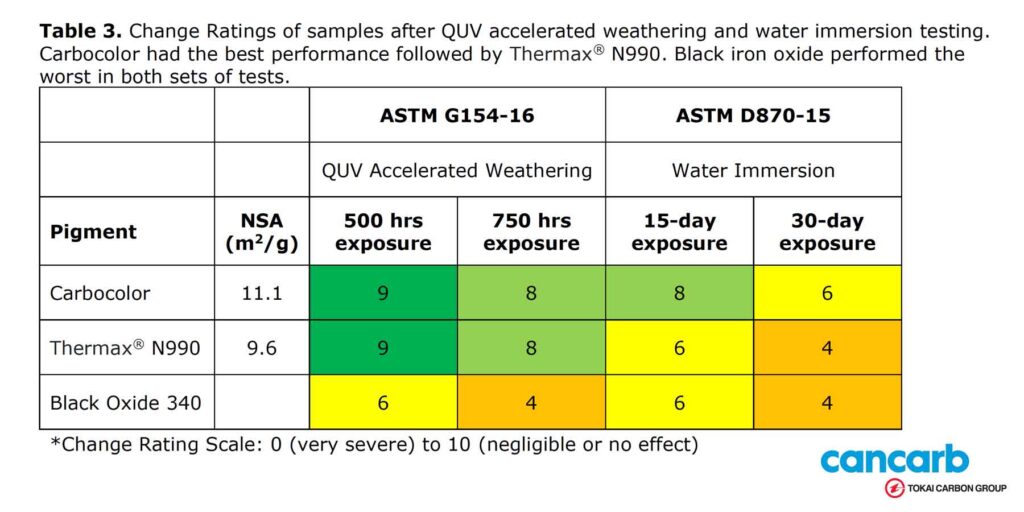
Tips for Using Carbocolor®:
- Measure out the appropriate quantity of pelletized Carbocolor®. This quantity is taken as a percentage of the total cementitious material in the concrete. The quantity of fly ash is to be included as part of the cementitious amount.
- Ensure that the Carbocolor® is incorporated into the mixer before the cement or aggregate material. Hand mixing is not recommended. If hand mixing is necessary, use powder grade Carbocolor® and mix vigorously.
- Allow at least 15 minutes of mixing time for maximum effectiveness.
- Carbocolor® has a tendency to deplete the level of air entrainment in concrete. Raise the level of air entrainment additive accordingly. Establishing the optimum amount of air entraining agent may require several trials.
- Have a large enough supply of water to dilute the mixture if necessary. The slump of the wet concrete is often higher when a pigment is used.
- Avoid performing pours in hot dry weather as it may cause cracking in the curing concrete.
- Avoid performing pours in wet, rainy weather as it will result in a spotty and unappealing surface finish.
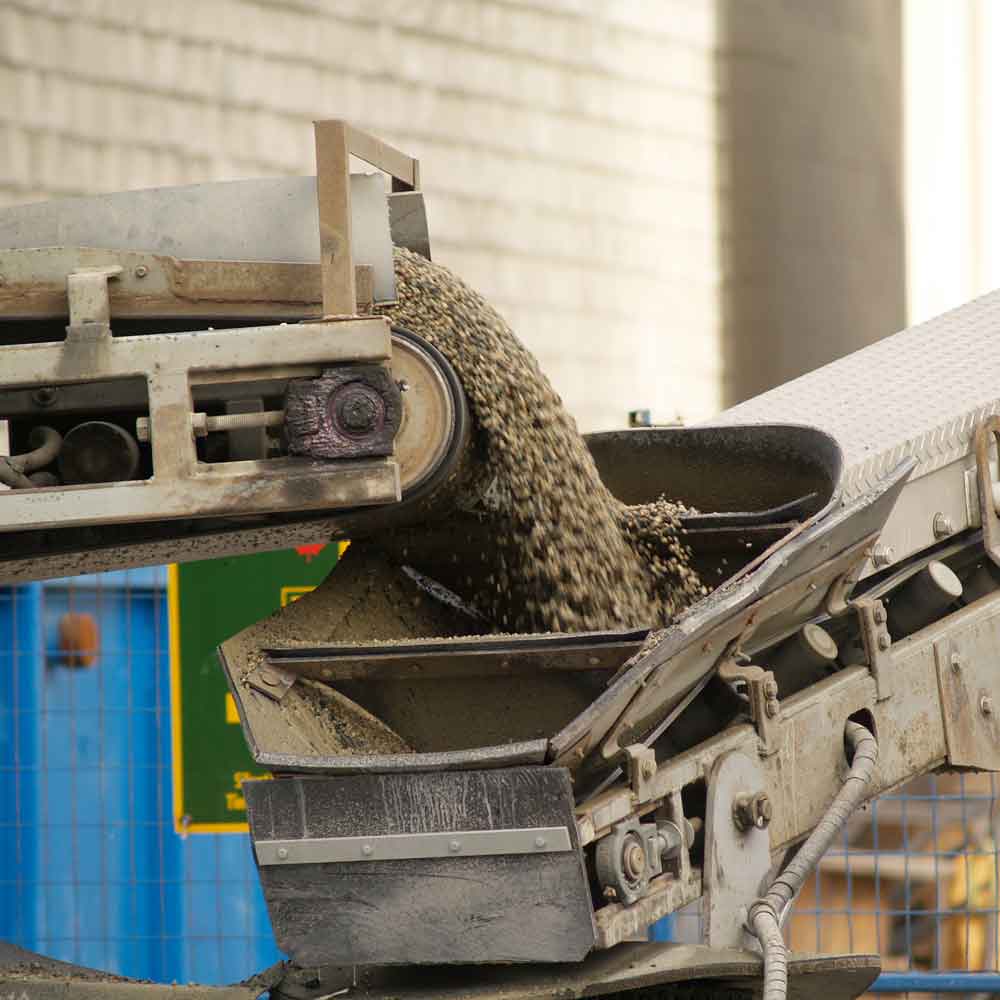
TECHnical bulletins